Moving Toward Ultra-Pure Hydrogen
Ivys’s Hydrogen Purification Solutions efficiently upgrade hydrogen-containing reformate, petrochemical process gas streams and refinery off-gas streams to pure and ultra-pure hydrogen. Ivys provides the most compact, economical and reliable PSA systems available today.
Our hydrogen purification systems have multiple applications for refineries, petrochemical plants, chemical plants or hydrogen producers, such as:
- Refinery Streams
- Steam Reformers
- Ethylene Off-gas
- Hydrogen Fuel Cells
- Partial Oxidation/Syngas
- Coke Oven Gas
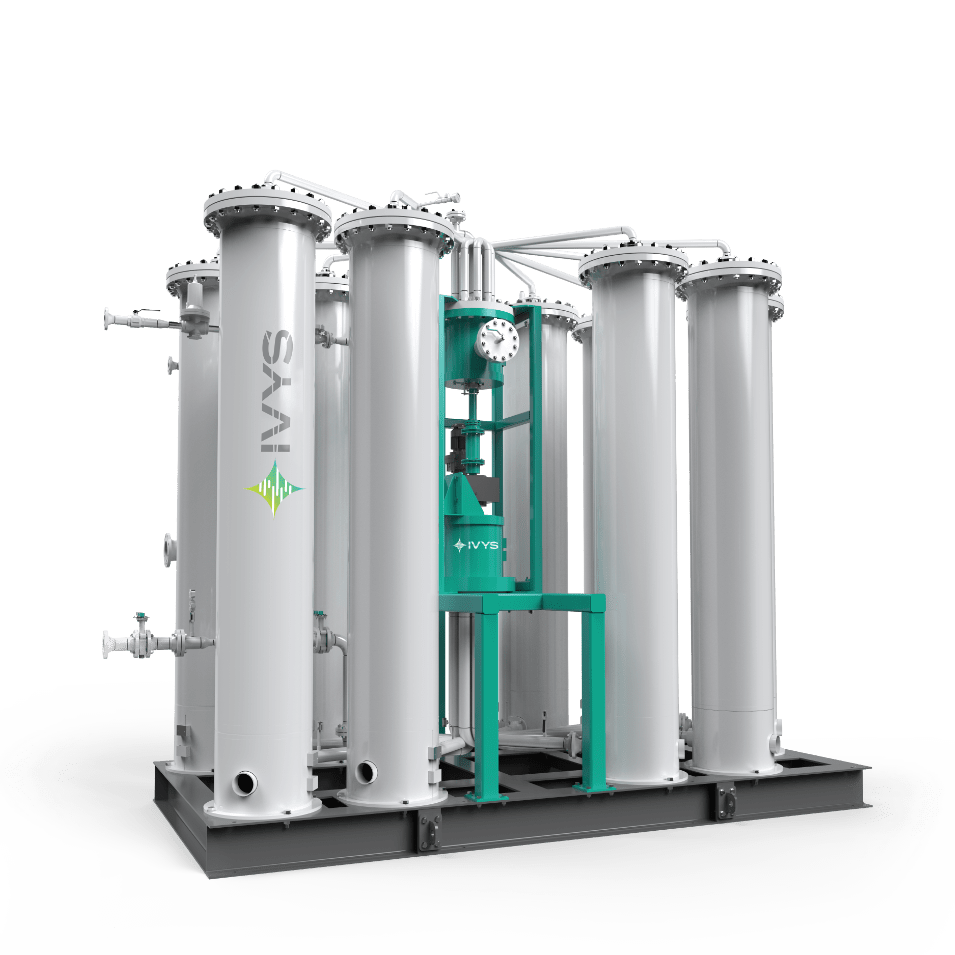
Features
Efficient, Reliable, Safe Operation
Ivys’ PSA systems offer unmatched proprietary advantages compared to conventional PSA systems.
These advantages include:
Compact
At least 3-5 times smaller compared to conventional PSA with the same capacity due to reduced PSA vessel size and the use of the rotary valves.
Easy and fast installation
Skid mounted systems with adsorbent preloaded in factory enable “plug-N-play” installation.
Simple control and operation
Only one parameter. The rotary valve speed needs to be controlled during normal operation.
Flexible capacity
Operation capacity can be matched by adjusting rotary valve speed to maximize recovery while meeting product purity requirements.
High recovery
Triple equalization cycle design ensures high product recovery.
Reliable
Availability is typically greater than 99.5 % due to the significantly reduced number of moving parts and long service intervals compared to conventional PSA systems.
Low OPEX
Electrical power is the only utility required for normal operation. Power consumption is typically less than 1 kW.
Hydrogen purification
Understanding
Ivys technology
System Configurations
H3100 G0 |
H3300 G1 |
H3200 G2 |
H3200 G3 |
H3200 G4 |
|
---|---|---|---|---|---|
Number of Beds | 6 | 8 | 9 | 9 | 9 |
Bed Diameter | 14”-48” | 3” | 2”-12” | 14”20” | 20”-42” |
Maximum Operating Pressure | 450 psig | 175 psig | 300 psig | 250 psig | 250 psig |
Feed Capacity (NCMH) | 1,200-15,500 | 10-45 | 25-950 | 1,450-3,100 | 4,500-29,000 |
Feed Gas Temp (°C) | 10-60 with 20-45 preferred | ||||
Design Standards | North America: ASME, NFPA, NEC, CSA / Europe: PED, ATEX, IEC | ||||
Voltage | 120Vac/1ph/60Hz, 240Vac/3ph/50 or 60Hz, 380Vac/3ph/50Hz, 480Vac/3ph/60Hz | ||||
Power Consumption | 0.2-0.5 kw typical | ||||
Design Life | 15+ years with scheduled maintenance, 10+years for adsorbents | ||||
Recommended Service | Inspection every 2.5 years; Minimum seal life 5 years |
Typical Hydrogen Source Gas
Feed Process Gas (vol%) | H2 | CO | CO2 | CH4 | CH2-3 | CH4 + | N2 | H2O Vapor |
---|---|---|---|---|---|---|---|---|
MSR SYNGAS | 60-80 | 0-10 | 10-20 | 0-10 | Sat. | |||
ATR SYNGAS | 40-60 | 0-10 | 15-25 | 0-10 | 0-30 | Sat. | ||
CPOX SYNGAS | 30-50 | 0-10 | 15-25 | 0-10 | 0-20 | Sat. | ||
GASIFICATION GAS | 20-60 | 0-20 | 0-20 | 0-20 | 0-10 | 0-5 | 0-10 | Sat. |
REFINERY OFF-GAS | 30-90 | 0-30 | 0-30 | 0-30 | 0-30 | 0-5 | Sat. | |
H2 POLISHING | 90-99 | Sat. | ||||||
AMMONIA CRACKING | 60-75 | 25-50 |
Performance
H2 PURITY | Up to 99.9999 % |
RECOVERY | 80-90 % typical. Recovery depends strongly on feed gas composition, pressure and product purity requirements. |
TURNDOWN | 40-100 % |
AVAILABILITY | Up to 99.9999 % |
APPLICATIONS |
|
Specifications
H-series Frame Size |
Vessel Outside Diameter |
Rotary Valve / # of Beds |
Max Op.Pressure | Feed Flow Capacity1 | Dimensions3 | Weight2 | ||||||||
---|---|---|---|---|---|---|---|---|---|---|---|---|---|---|
Width | Depth | Height | ||||||||||||
PSIG | BARG | SNFM | Nm3/hr | ft | m | ft | m | ft | m | lbs | kgs | |||
H-3100 | 14" | G0-6BED | 450 | 31 | 750 | 1,200 | 10.5 | 3.2 | 9.0 | 2.7 | 12.0 | 3.6 | 15,000 | 6,800 |
16" | 1,000 | 1,600 | 10.7 | 3.3 | 9.3 | 2.8 | 12.0 | 3.6 | 16,000 | 7,300 | ||||
18" | 1,250 | 2,000 | 10.9 | 3.3 | 9.3 | 2.8 | 12.0 | 3.6 | 17,000 | 7,700 | ||||
20" | 1,600 | 2,550 | 11.1 | 3.4 | 9.5 | 2.9 | 12.0 | 3.6 | 19,000 | 8,600 | ||||
24" | 2,300 | 3,700 | 11.6 | 3.5 | 10.0 | 3.0 | 12.0 | 3.6 | 21,000 | 9,500 | ||||
30" | 3,900 | 6,000 | 12.6 | 3.8 | 11.0 | 3.3 | 12.0 | 3.6 | 24,000 | 11,000 | ||||
36" | 5,350 | 8,500 | 13.6 | 4.1 | 12.0 | 3.6 | 16.2 | 4.9 | 28,000 | 17,000 | ||||
42" | 7,400 | 11,700 | 14.6 | 4.4 | 13.0 | 4.0 | 16.2 | 4.9 | 32,000 | 14,500 | ||||
48" | 9,800 | 15,500 | 15.6 | 4.7 | 14.0 | 4.3 | 16.2 | 4.9 | 36,000 | 16,300 | ||||
H-3200 | 2" | G2-9BED | 300 | 21 | 15 | 25 | 4.7 | 1.4 | 3.7 | 1.1 | 7.6 | 2.3 | 3,850 | 1,750 |
4" | 65 | 100 | 4.7 | 1.4 | 3.7 | 1.1 | 7.6 | 2.3 | 3,900 | 1,800 | ||||
6" | 145 | 230 | 4.7 | 1.4 | 3.7 | 1.1 | 7.6 | 2.3 | 4,550 | 2,050 | ||||
8" | 275 | 430 | 5.3 | 1.6 | 5.3 | 1.6 | 9.5 | 2.9 | 4,900 | 2,200 | ||||
10" | 420 | 670 | 5.5 | 1.7 | 5.3 | 1.6 | 9.5 | 2.9 | 5,100 | 2,300 | ||||
12" | 600 | 950 | 6.3 | 1.9 | 5.8 | 1.8 | 9.5 | 2.9 | 5,400 | 2,450 | ||||
H-3200 | 14" | G3-9BED | 250 | 17 | 900 | 1,450 | 18.4 | 5.6 | 8.4 | 2.6 | 13.6 | 4.1 | 18,500 | 8,400 |
16" | 1,200 | 1,950 | 18.6 | 5.6 | 8.5 | 2.6 | 13.6 | 4.1 | 20,000 | 9,100 | ||||
18" | 1,600 | 2,550 | 18.8 | 5.7 | 8.8 | 2.7 | 13.6 | 4.1 | 21,500 | 9,800 | ||||
20" | 1,950 | 3,100 | 19.0 | 5.8 | 9.0 | 2.7 | 13.6 | 4.1 | 23,000 | 10,500 | ||||
H-3200 | 24" | G4-9 BED | 250 | 17 | 2,800 | 4,500 | 21.0 | 6.4 | 10.5 | 3.2 | 14.0 | 4.3 | 28,000 | 12,700 |
30” | 4,500 | 7,100 | 23.5 | 7.2 | 12.0 | 3.6 | 14.0 | 4.3 | 32,500 | 14,750 | ||||
36” | 6,650 | 10,500 | 27.0 | 8.2 | 13.5 | 4.1 | 18.3 | 5.6 | 37,000 | 16,800 | ||||
42” | 8,850 | 14,000 | 30.0 | 9.1 | 15.0 | 4.6 | 18.3 | 5.6 | 41,500 | 18,850 | ||||
48” | 11,700 | 18,500 | 33.0 | 10.1 | 16.5 | 5.0 | 18.3 | 5.6 | 46,000 | 20,900 | ||||
54” | 14,900 | 23,500 | 37.0 | 11.3 | 18.0 | 5.5 | 18.3 | 5.6 | 52,000 | 23,600 | ||||
60” | 18,350 | 29,000 | 42.0 | 12.8 | 19.5 | 5.9 | 18.3 | 5.6 | 57,000 | 25,900 | ||||
H-3300 | 3" | G1-9 BED | 175 | 12 | 28 | 45 | 2.6 | 0.9 | 2.8 | 0.9 | 7.3 | 2.2 | 1,500 | 700 |
1Specifications listed above are typical values. Each PSA will be sized individually to customer process requirements.
2Weight = empty
3Dimensions don’t include surge tanks which are sized based on customer process data