The Importance of Regular Filter Changes in Industrial Air Compressors
Industrial air compressors are the unsung heroes of many manufacturing and production processes. These machines provide the compressed air that powers the tools, machinery, and systems in industries such as automotive, aerospace, food and beverage, pharmaceuticals, and construction. To keep these heroes operating at their best, one of the most crucial maintenance tasks is regularly replacing their filters. This article dives into the why and how of this essential task, explaining its role in operational efficiency, cost savings, and equipment longevity.
Protecting the Compressor, Downstream Equipment and Products
The primary function of air compressor filters is to remove contaminants from the air before they enter the compressor, reach downstream equipment, or spoil products. Contaminants such as microorganisms, dust, dirt, moisture, and oil can severely damage the compressor and other connected machinery. Over time, if these particles are not filtered out, they can accumulate within the compressor, leading to internal wear and tear, corrosion, and potential system failures.
For instance, particles can cause abrasive wear on the compressor’s moving parts, leading to increased friction and heat generation. This can result in premature component failure, requiring costly repairs or even replacing the entire compressor. Similarly, if contaminants reach downstream equipment, they can cause corrosion in storage vessels, overall air distribution systems, and blocked valves, cylinders, and motors. In the food, beverage, and pharmaceutical industry especially, products themselves may become contaminated, spoiled, or damaged, leading to significant financial losses and potential harm to consumers.
The potential risks of not changing filters are significant. Understanding these risks is crucial as it underscores the importance of this maintenance task. It’s not just about preventing wear and tear on the compressor, but also about protecting downstream equipment and products, and ensuring the smooth operation of the entire system.
Regularly changing filters can significantly reduce the risk of contaminants entering the compressor and downstream systems. This not only extends the lifespan of the equipment but also ensures optimal performance, saves costs, and prevents potential system failures. Reassure yourself and your team that this maintenance task is effective and crucial for the smooth operation of industrial air compressors.
Maintaining Air Quality Standards
Maintaining clean and contaminant-free compressed air is essential in industries where air quality is critical, such as food and beverage production, pharmaceuticals, and electronics manufacturing. Poor air quality can compromise product integrity, safety, and compliance with industry regulations.
Air compressor filters are designed to remove various contaminants, including particulate matter, oil vapor, and moisture. However, over time, these filters become saturated and lose their effectiveness. When filters are not changed regularly, contaminants can bypass the filtration system, leading to degraded air quality.
System engineers use ISO 8573-1:2010 as the standard to classify the level of air purity. Filters are specially designed and tested to meet these rigorous standards so system operators can choose the appropriate quality to address their purification needs depending on the application and environment.
Regular filter changes ensure that the air compressor continues to deliver high-quality compressed air that meets industry standards and regulations. This is particularly important in sensitive applications where even minor contamination can have significant consequences.
Improving Energy Efficiency
Dirty or clogged filters can significantly reduce an air compressor’s efficiency. When filters become clogged, the compressor has to work harder to maintain the required air pressure. This increased workload increases energy consumption, leading to higher operational costs. Clogged filters can cause energy consumption to increase by up to 20% in compressed air systems. This can result in higher energy bills and a larger carbon footprint, which may be concerning for companies aiming to reduce their environmental impact.
By regularly changing filters, you can ensure that the air compressor operates at optimal efficiency, reducing energy consumption and lowering operational costs. Additionally, maintaining energy efficiency can help companies achieve sustainability goals and improve overall environmental performance.
Preventing Unscheduled Downtime
Unscheduled downtime can be very costly for any industrial operation. If an air compressor fails due to lack of maintenance, such as not changing filters, it can stop production entirely. The cost of lost production, emergency repairs, and potential damage to other equipment can quickly add up, impacting profitability.
Regular filter changes are a proactive maintenance measure that can prevent unexpected breakdowns and extend the intervals between major maintenance tasks. Keeping filters clean and functional reduces the risk of compressor failure and unscheduled downtime, ensuring that production runs smoothly and efficiently.
Cost Savings in the Long Term
While changing filters may seem like a minor maintenance task, it can lead to significant cost savings in the long run. The cost of replacing filters is minimal compared to the expenses associated with compressor repairs, component replacement, or lost production time due to equipment failure.
Regular filter maintenance also contributes to the overall health of the compressed air system, reducing the likelihood of major repairs and extending the compressor’s lifespan. This means lower maintenance costs over time and a better return on investment for your equipment.
Compliance with Manufacturer Warranties
Many air compressor manufacturers include maintenance requirements, including regular filter changes, in their warranties. Failing to adhere to these maintenance guidelines can void the warranty, leaving you responsible for the full cost of any repairs or replacements.
By following the manufacturer’s recommended maintenance schedule, including timely filter replacements, you ensure that your warranty remains valid. This provides peace of mind and financial protection in case of any unexpected issues with the compressor.
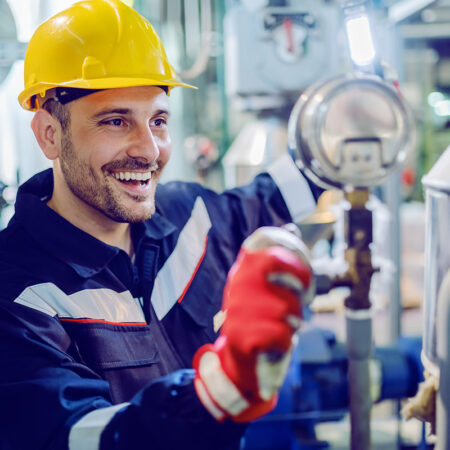
Regular filter changes are crucial for industrial air compressors to operate efficiently and reliably. They help shield the compressor and downstream equipment from damage, maintain air quality standards, enhance energy efficiency, prevent unexpected downtime, and save costs in the long term. By including filter maintenance in your routine equipment upkeep, you can guarantee that your air compressor maintains peak performance, supporting the smooth and efficient operation of your industrial processes.
Ivys distributes a wide range of air compressor filters compatible with over 250 brands and 12,000 parts available at competitive prices.
Ivys’s alternative parts are very competitively priced.
Download a price list and compare.
Contact our compressed air filter experts, who are available to help you select the right replacement filter.