How to choose the right compressor – 7 key factors
Compressors are used in various industries, and there are many types, sizes, and brands available on the market, making it challenging to select the right one. When evaluating our clients’ air compression needs, Ivys’s compressed air specialties consider the following seven key factors.
1. Compressor Capacity and Size
Picking the best air compressor for your facility is essential to keep production running smoothly and save energy costs.
What will your compressor be used for, how many tools will be needed, and what flow will be required? Evaluate the PSI requirements of the tools and processes for your application and facility.
Air audits are an excellent way of determining a plant’s compressed air utilization. A wealth of data is available to calculate your capacity requirements, and our compressor solutions experts can help you evaluate your needs.
2. Duty cycle & utilization
The duty cycle refers to the amount of time a compressor is expected to run at total capacity each hour. Will your compressor need to run all day or occasionally?
When choosing a compressor with the best life cycle cost, consider the following guidelines.
- If usage is less than 4 hours/day, choose a reciprocating compressor.
- For usage between 4 and 8 hours/day, a belt-driven screw compressor is recommended.
- If usage exceeds 8 hours/day, a direct-driven screw compressor is the most suitable option.
3. Quality of Air
Industrial compressors use oil to cool, lubricate, and seal moving parts, exposing compressed air to the oil.
The selection of the air compressor will vary depending on your specific application requirements.
In specific applications, compressed air comes into direct contact with products such as food and pharmaceuticals, making oil-free air the preferred choice.
For critical and sensitive applications, choose a compressor with class zero air, free from oil residue all the time.
How much maintenance will be required will depend on your application and choice of compressor.
4. Maintenance requirements
How often consumables need to be replaced will determine how much time must be dedicated to their replacement.
Is the compressor designed for easy access to components to minimize service time?
When comparing compressors, there are several elements that can reduce maintenance time.
Two-stage filtration will increase the life of the consumables when compared with single-stage filtration, increasing uptime between scheduled maintenance and, in turn, increasing productivity.
Other features also reduce maintenance. For example, a non-touchless rotor will perform consistently throughout the compressor’s life.
Factors like open or closed loop water circuits for cooling are also important for maintenance considerations. Closed loop systems eliminate the need for a water purifier on the inlet, making it one less filter to change. Auto-water replenishment systems, such as the Elgi AB series, reuse the condensate water to auto-replenish the tanks with fresh, clean water.
3. Quality of Air
Industrial compressors use oil to cool, lubricate, and seal moving parts, exposing compressed air to the oil.
The selection of the air compressor will vary depending on your specific application requirements.
In specific applications, compressed air comes into direct contact with products such as food and pharmaceuticals, making oil-free air the preferred choice.
For critical and sensitive applications, choose a compressor with class zero air, free from oil residue all the time.
How much maintenance will be required will depend on your application and choice of compressor.
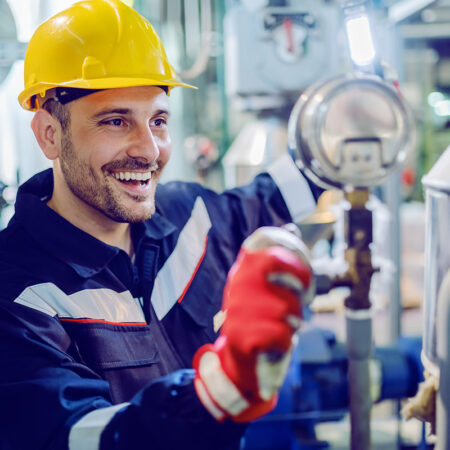
Regular filter changes are crucial for industrial air compressors to operate efficiently and reliably. They help shield the compressor and downstream equipment from damage, maintain air quality standards, enhance energy efficiency, prevent unexpected downtime, and save costs in the long term. By including filter maintenance in your routine equipment upkeep, you can guarantee that your air compressor maintains peak performance, supporting the smooth and efficient operation of your industrial processes.
Ivys distributes a wide range of air compressor filters compatible with over 250 brands and 12,000 parts available at competitive prices.
Ivys’s alternative parts are very competitively priced.
Download a price list and compare.
Contact our compressed air filter experts, who are available to help you select the right replacement filter.